3D Printing for Complex Propeller Models
When producing molds for propeller casting, the standard method involves using robots that directly mill the sand with the desired geometry. This approach is fast, precise, and efficient—provided the geometry allows it.
However, in certain cases we encounter especially complex designs, such as propellers with overlapping blades. This configuration is commonly found in cargo vessels with very high power-to-draft ratios, where performance needs to be maximized under specific operating conditions. In these cases, robotic milling is not feasible, as the robot arms cannot properly access certain areas of the mold without causing damage.
Traditionally, the solution was to create wooden models using CNC milling, followed by manual sanding and painting. This process is slower and demands significant expertise to achieve the required level of precision.
At Rice Propulsion, we have introduced 3D printing as an alternative for these scenarios.
This technology allows us to produce high-precision models, even with complex or large-scale geometries, eliminating the need for manual finishing. As a result, we reduce production times, improve the quality of the final product, and maintain full control over the entire process.
Moreover, since these are single-use models, being able to manufacture them quickly and efficiently is key to staying competitive and meeting the specific needs of each project.
3D printing enables us to adapt our processes to any geometric challenge while maintaining the quality standards required by the marine industry.
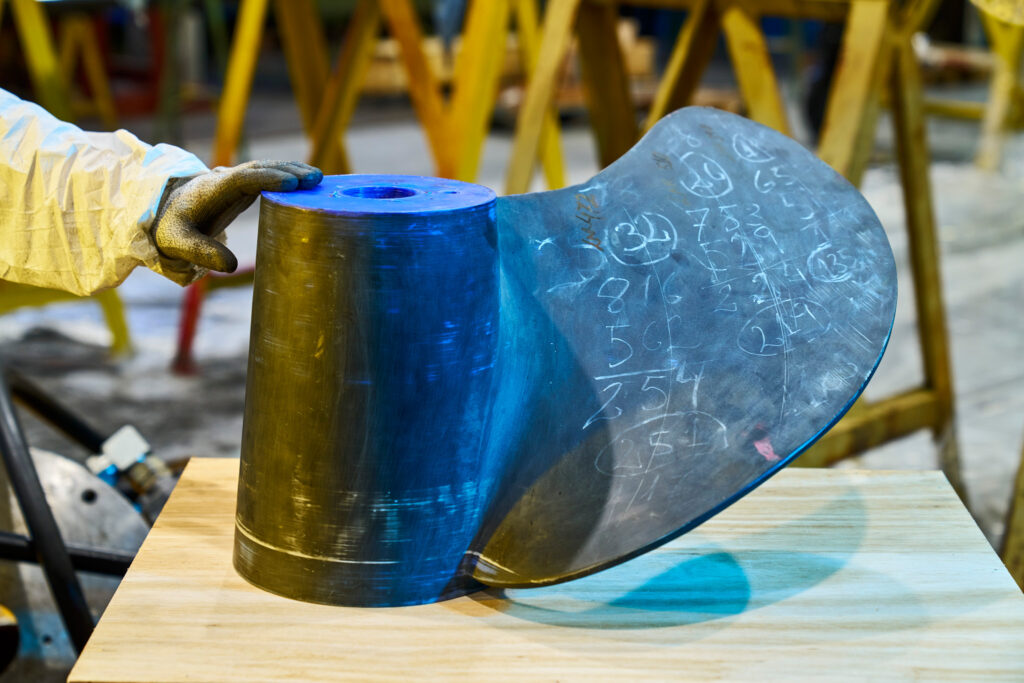
- Propellers
- Hydrodynamic, R&D