Propeller Manufacturing
propeller Manufacturers Specialized in bronce casting
At Rice Propulsion, our state-of-the-art propeller manufacturing facilities enable us to produce over 1,600 tons of finished products annually, delivering precise and efficient production of naval components.
Propeller Manufacturers in Europe, Supplying the World
Our foundry, specializing in propeller manufacturing, is located in Spain, in Vilagarcía de Arousa, just 50 km from Vigo, home to the most important port in the northwest of the country, ensuring excellent connections by land, sea, and air.
As leading propeller manufacturers, we supply fixed-pitch propellers weighing up to 18 tons and with diameters up to 5,200 mm.
Our controllable pitch blades can be manufactured in virtually any size up to 18 tons and diameters up to 9,000 mm, ranging from maneuvering propeller blades to main propulsion blades for military applications or large cruise ships.
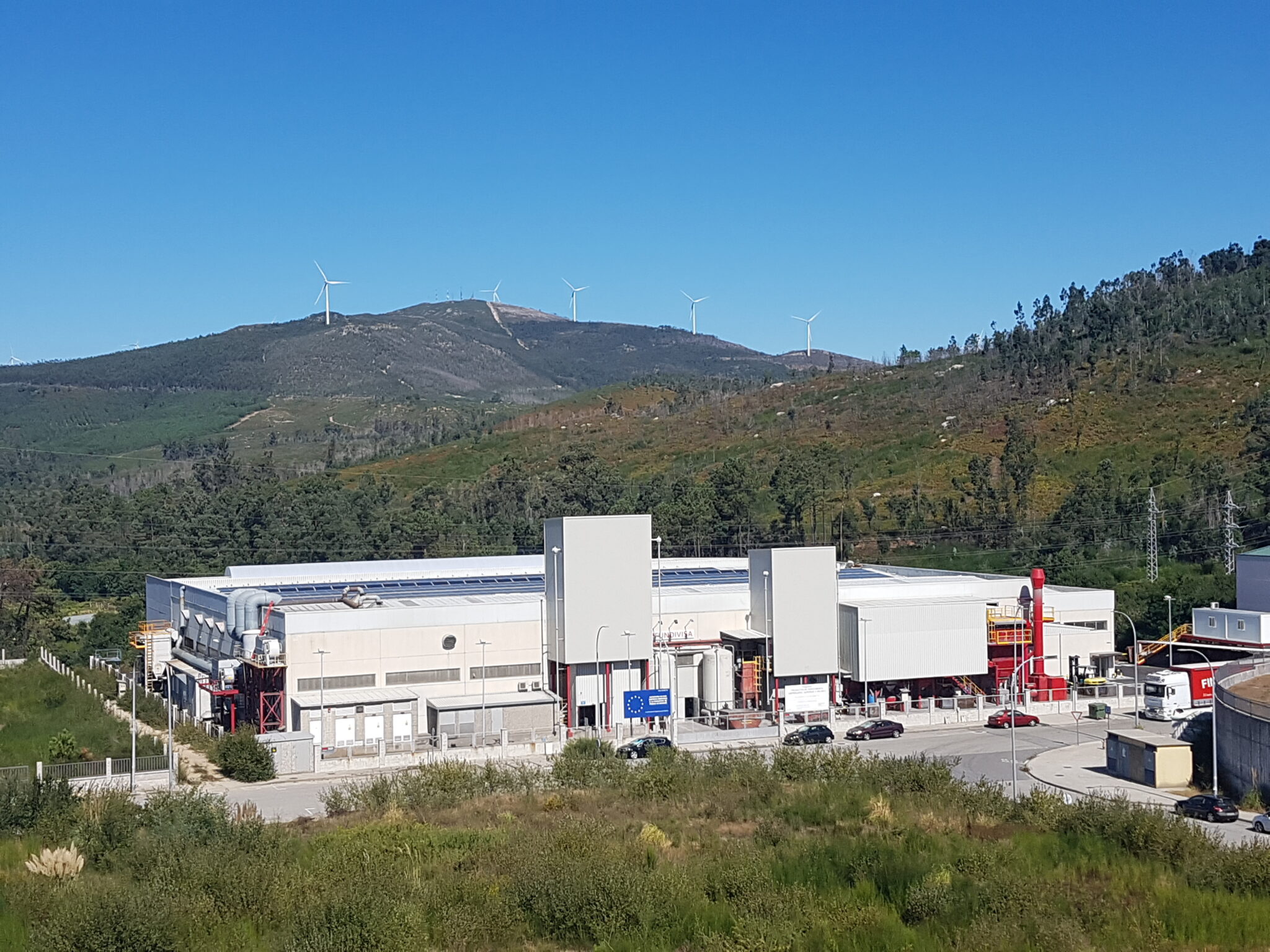
Propeller Manufacturing Process
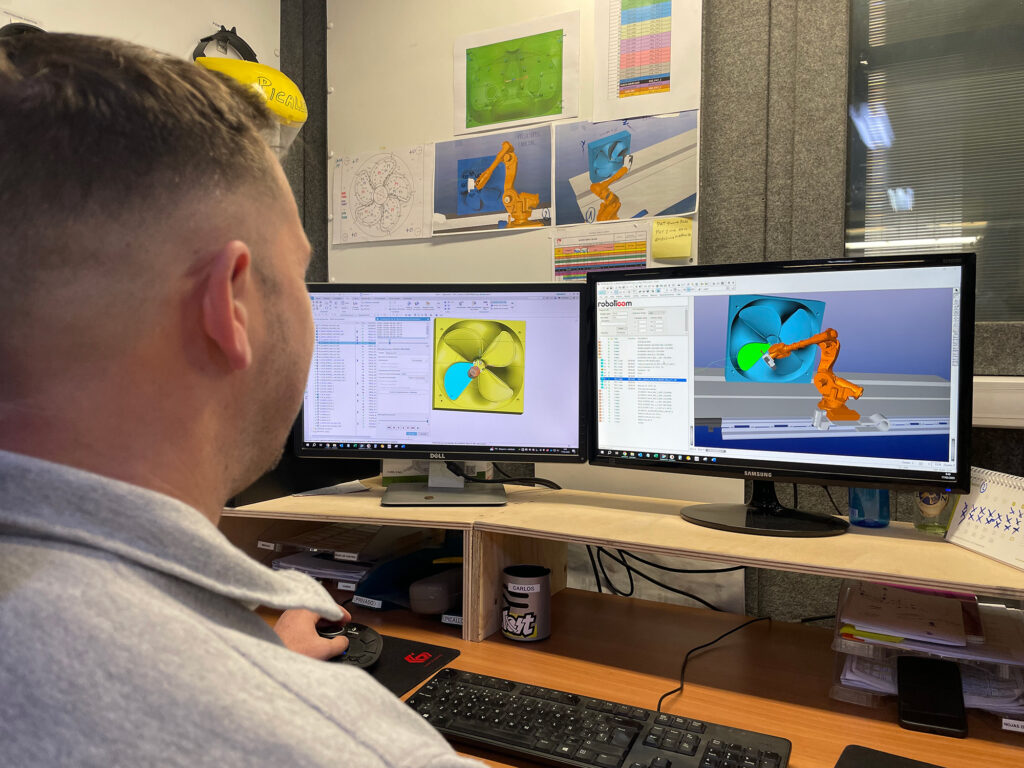
The manufacturing process of our propellers begins with the engineering phase, where we process the 3D model and develop a production plan tailored to the design. Using CAM (Computer-Aided Manufacturing) technology, we program our robots to work directly with the models provided by the engineering department.
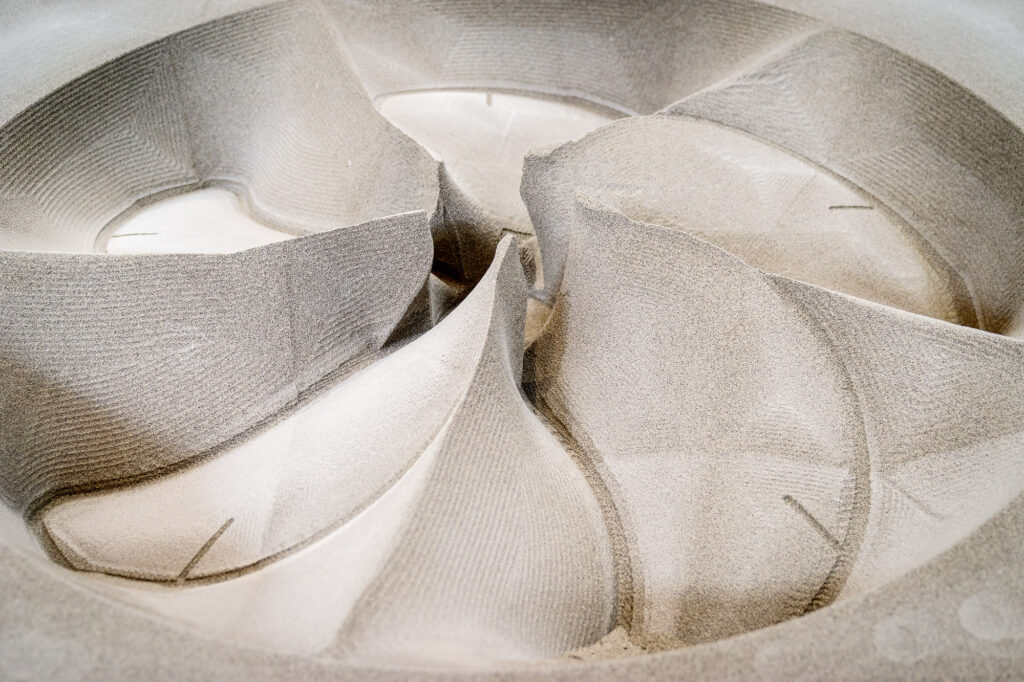
Once the production process is defined, we move on to the molding stage, where we utilize robotic molding cells to create molds without the need for traditional wooden patterns. Even if we work in both ways, this technology significantly reduces production time and ensures superior precision in the propeller’s shape.
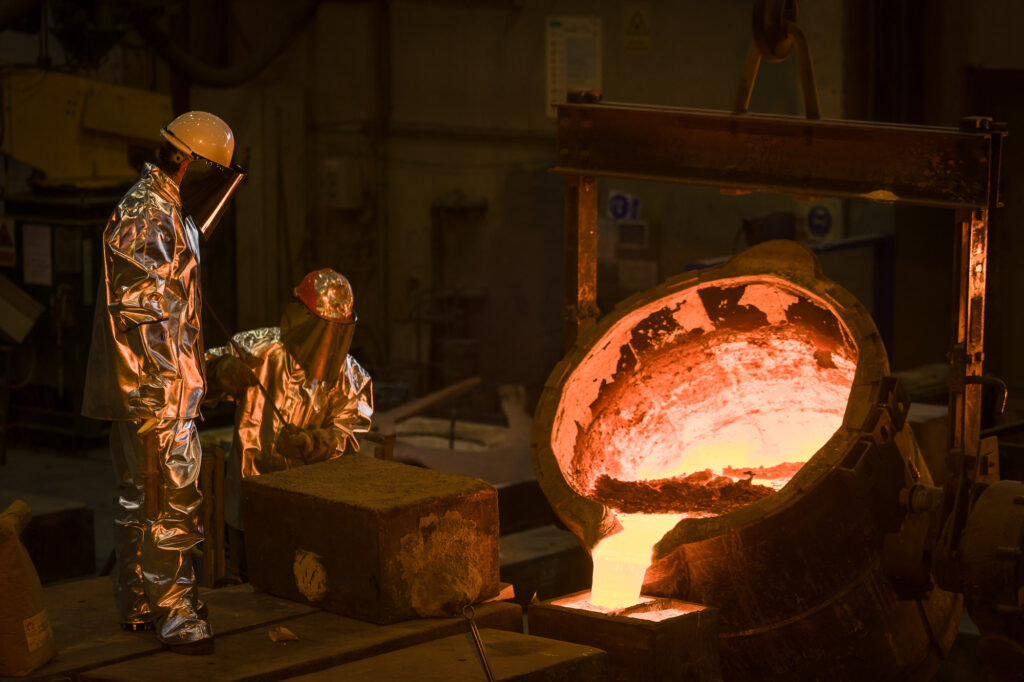
We employ rigorous casting processes that allow us to produce high-quality components tailored to each client's specific needs. Our facilities are equipped with electric induction furnaces and patternless robotized cells.
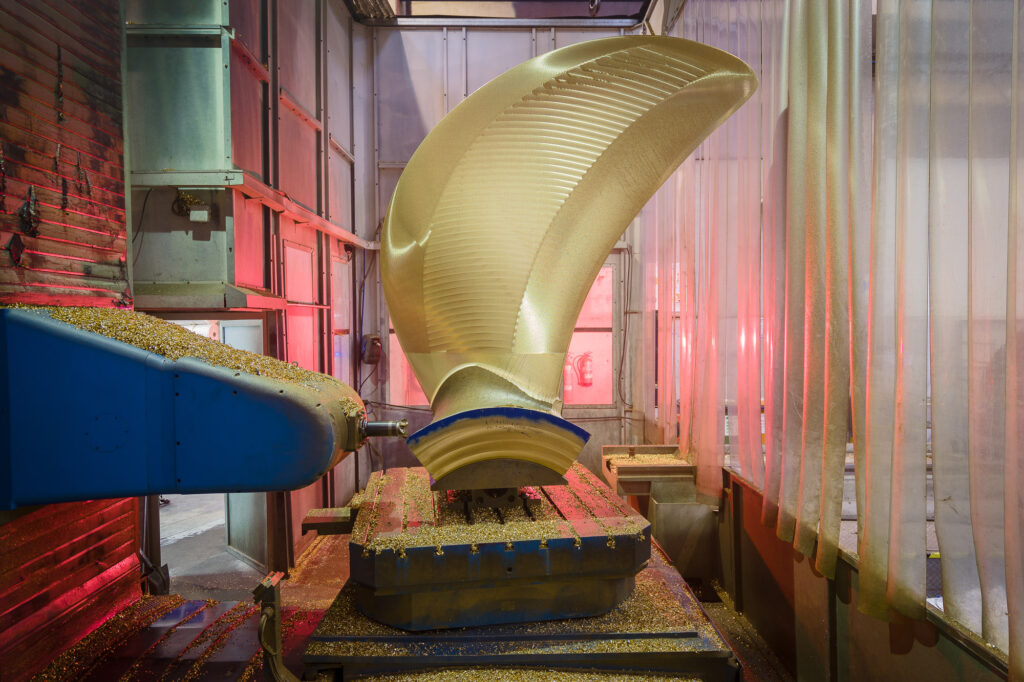
Our advanced machining center features CNC-controlled machines, the hydraulic surfaces are obtained in CNC 5-axis milling machines, and several CNC lathes capable of handling up to 4.3 meters in diameter.
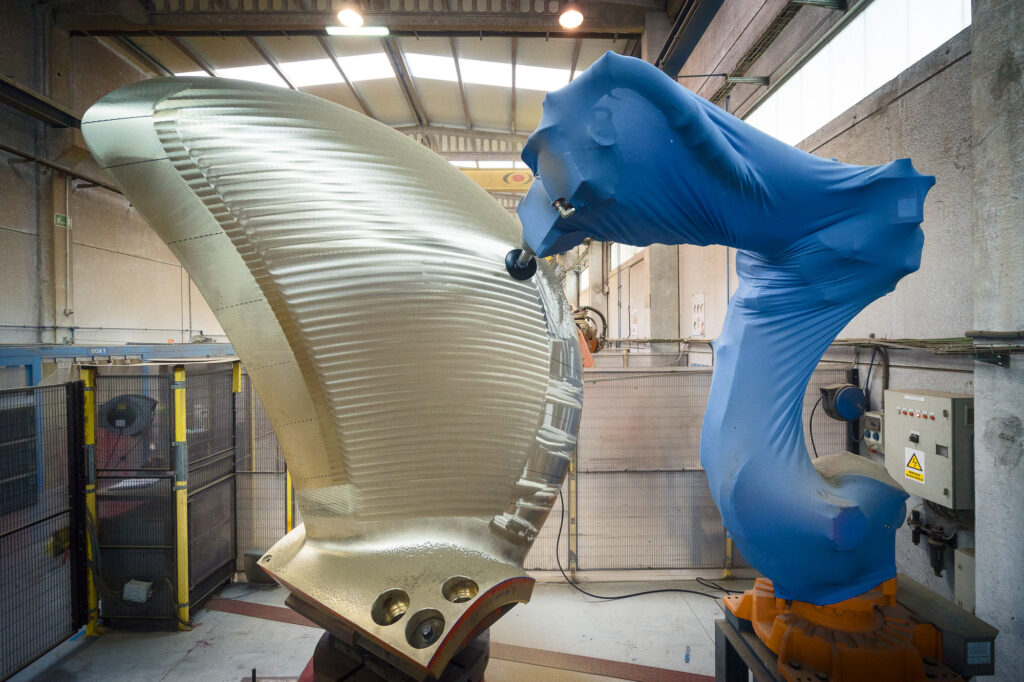
To ensure smooth surfaces and optimal finishes that enhance both performance and aesthetics, we combine automated and manual propeller manufacturing process. CNC controlled robots do most of the polishing work, while our skilled workers give the final touch by hand.
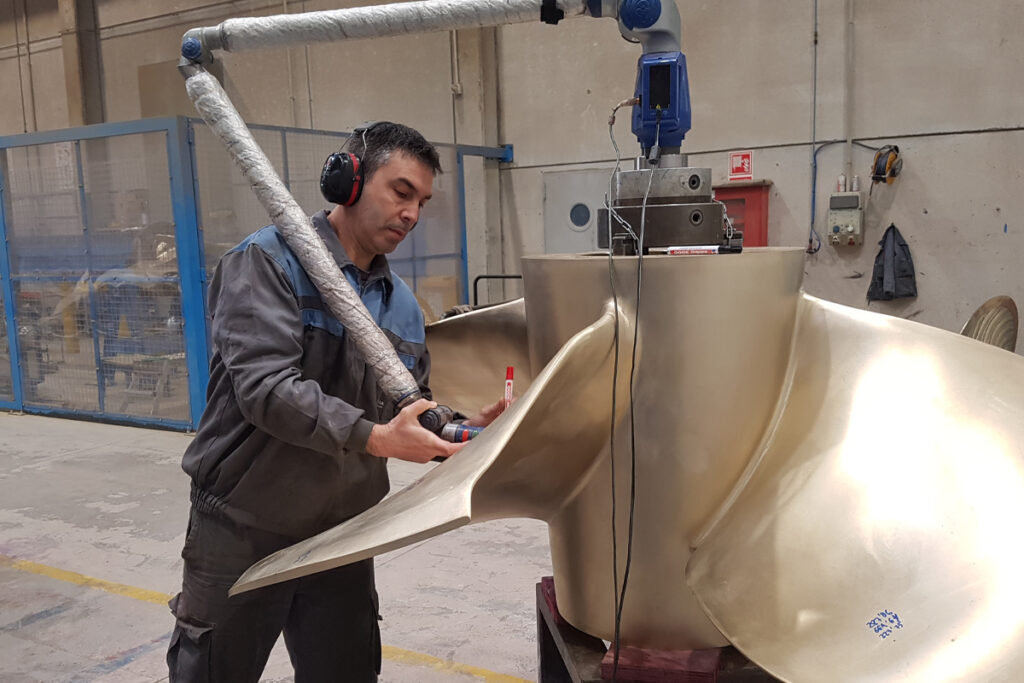
Every piece we manufacture undergoes a rigorous dimensional control process to meet the most demanding standards in the maritime industry. We have a laboratory available with a spectrometer for chemical analysis and tensile strength machine. We have as well static and dynamic balancing equipment.
Need an expert team of propeller manufacturers? Let’s talk!
Learn More From
Frequently Asked Questions
As leading propeller manufacturers, we use high-quality materials to ensure durability, efficiency, and corrosion resistance. Our propeller manufacturing process includes bronze alloys (Cu3 aluminum bronze, Cu1 manganese bronze) and stainless steel (CF3), carefully selected based on vessel type, operational conditions, and performance requirements.
Yes, as propeller manufacturers, we specialize in custom propeller manufacturing based on vessel specifications such as engine power, RPM, vessel weight, operating conditions, and hydrodynamic efficiency. Our engineering team uses Computational Fluid Dynamics (CFD) and advanced casting and machining techniques to optimize performance and fuel efficiency.
Our foundry produces fixed-pitch marine propellers up to 18 tons and with diameters reaching 5,200 mm. For controllable-pitch blades, we can manufacture sizes up to 9,000 mm in diameter, catering to a wide range of vessels, from maneuvering propellers to main propulsion blades for military ships and cruise liners.
Yes, as global propeller manufacturers, we supply ship propellers worldwide. Our propeller manufacturing facility ensures efficient logistics and secure transportation, allowing us to deliver custom-made ship propellers to clients globally, whether for commercial vessels, military ships, or industrial applications.
Choosing the right propeller is crucial for fuel efficiency, vessel performance, and durability. Factors to consider include:
- Engine power and RPM – Ensures compatibility with the vessel’s propulsion system.
- Propeller pitch and diameter – Impacts thrust, speed, and efficiency.
- Number of blades – Affects noise levels, vibration, and hydrodynamic performance.
- Material selection – Stainless steel for high-impact resistance, bronze for corrosion resistance.
Our expert propulsion engineers can guide you in selecting the ideal propeller design based on your vessel’s requirements.
To receive a custom propeller manufacturing quote, you can complete our propeller questionnaire.